TM 10-4320-307-24
3-34
CAM FOLLOWER INSPECT REPAIR/REPLACE (CONT).
g.
Visually Inspect cam follower bushing for breaks, cracks, or out of round condition.
h.
Use inside micrometers to measure inside diameter of bushing. Bushing must measure 0.7501 to 0.7511 inch
(19.053 to 19.078 mm). Replace bushing if it measures more than 0.752 Inch (19.10 mm).
i.
Visually inspect cam follower levers for breaks and cracks.
j.
Visually check push tube insert by using a new push tube. Coat ball end with prussian blue. Place ball end of
push tube into push tube insert and rotate. If wear area is not 80 percent blued. replace push tube insert.
k
Visually inspect cam follower roller pin for cracks or out of round condition. Measure outer diameter with
micrometer. Replace if outer diameter is less than 0.497 inch (12.62 mm).
I.
Visually inspect exhaust and intake valve cam rollers for breaks, cracks, or out of round condition. Set
telescoping gage to 0.503 inch (12.83 mm). Place gage into inner diameter of roller. If gage slides into roller
it is worn beyond wear limit and must be replaced. Measure outer diameter with a micrometer. If outside
diameter of roller is less than 1.248 inches (31.71 mm). replace.
m.
Visually inspect fuel injector cam rollers for breaks, cracks. or out of round condition. Set telescoping gage
to 0.505 inch (12.78 mm). Place gage into inner diameter of roller. If gage slides into roller it is worn beyond
wear limit and must be replaced. Measure outer diameter with micrometer If outer diameter of roller is less
than 1.248 inches (31.71 mm), replace.
n.
Visually inspect the cam follower shaft for cracks and defects. Measure the outside diameter of the shaft.
Replace the shaft if it measures less than 0.748 inch (19 mm). Normal diameter should be 0.7485 inch to
0.7490 inch (18.012 to 19.02 mm).
NOTE
If the rollers are damaged, be sure to inspect the camshaft for damage. Replace any part of that is
damaged or worn beyond the limits.
2.
Clean, inspect, and repair pushrods as follows:
a.
Clean pushrods with dry cleaning solvent and dry with compressed air.
b.
Visually inspect all and socket ends of pushrods for uneven wear or scratches.
c.
Inspect straightness of pushrod by rolling it on a level bench. Replace pushrod If bent.
d.
Inspect for engine oil in pushrods as follows:
(1)
Hold pushrod horizontally and drop it from a height of 6 inches on concrete floor or metal surface.
(2)
The pushrod may be used if a ringing sound Is heard.
(3)
If a dull (or non-ringing) sound is heard, the pushrod contains engine oil and must be discarded
3-124
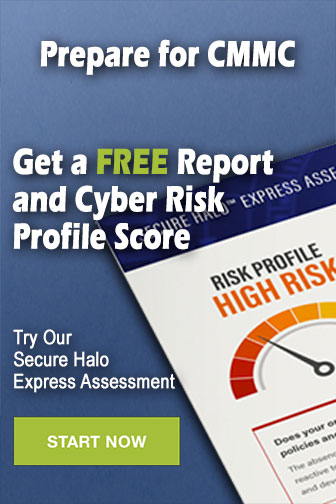