TM 10-4320-307-24
4-12
CYLINDER HEAD ASSEMBLY REPAIR (CONT).
10.
Inspect valve spring working length as follows:
a.
Compress spring to 1.724 inches (43.79 mm) working length.
b.
Check that force required to compress spring to working length is between 162.75 and 147 lbs (724 and 655
N).
c.
Discard springs not within limits of step b.
11.
Inspect crosshead guides. Outside diameter of crosshead guides must not be worn smaller than 0.432 inch
(10.97 mm).
12.
Inspect crosshead guides for straightness. Crosshead guides must be at a right angle to surface at cylinder
head. Replace any guide that is not straight.
13.
Inspect surface of cylinder head around water holes. The holes must not have any scratches, cracks. or
corrosion deeper than 0.003 inch (0.08 mm). There must not be any defect which extends more than 0.094 inch
(2.38 mm) from edge of water hole.
14.
Inspect injector sleeve for evidence of coolant leakage. Check sleeve for scratches or other damage.
15.
Inspect valve seat area width (1). If width Is more than 0.125 inch (3.18 mm) and cannot be cut narrower,
replace insert.
REPAIR:
1.
The cylinder head surface must be repaired if it
has scratches, damage, or is worn so that surface
is not even. Use milling machine to cut surface.
Keep surface at 125 micro-inch. Use venire
depth gauge or micrometer to check height of cyl-
inder head. Do not remove more than 0.005 inch
(0.13 mm) material with each cut. The cylinder
head height must not be less than 4.340 inches
(110.24 mm).
2.
Grind valve seats (1) to a minimum of 0.063 inch
(1.59 mm) to a maximum of 0.125 inch (3.18 mm).
After grinding valve seats, clean cylinder head in
accordance with CLEANING procedure this task.
Use a 1/2 inch (13.7 mm) bristle brush to clean the
valve guide inside diameter.
3.
Repair damaged valve guide bores by reaming
bore to measure 0.760 to 0.761 inch (19.30 to
19.33 mm) inside bore. Remove sharp edges and
install oversize valve guide in cylinder head.
4.
Repair valves by grinding valve face to an angle
exactly 30 degrees from the horizontal position of
the valve.
5.
Lap valves using valve lapping compound.
6.
Using prussian blue, make sure valve face has
correct contact against valve seat.
4-91
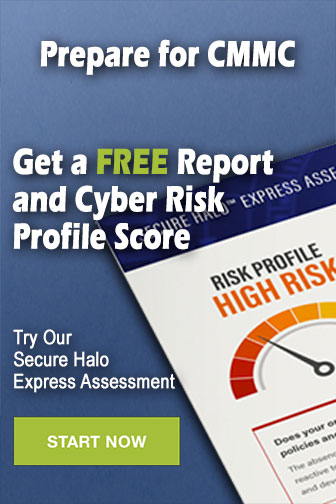