TM 5-4930-227-14
Section Il. TANK AND FRAME
6-9. Tank and Frame
The tank shells are of durable aluminum con-
struction; the frame is of welded sheet metal.
The tank and f rames will require a minimum of
maintenance. Make certain every precaution is
taken prior to attempting any repair on a tank.
6-10. Welding Repairs
a. Tanks. No repair will be initiated until the
tank has been thoroughly vented and cleaned. Ob-
serve necessary precautions and weld the dam-
aged area in accordance with standard tech-
niques, Refer to paragraph 6-10d for welding
precautions.
b. Frame. Make certain the frame is free of
dirt, oil, grease, or other foreign matter, and
bare metal is exposed for welding. Remove neces-
sary components before welding.
c. Tank Cleaning. The tank must be free of
explosive vapors and thoroughly cleaned before
any repairs are attempted; drain the tank of all
contents and open filler plug, allow filler to re-
main open for several minues. If compressed air
is available, blow out the tank. Clean the tank in-
terior with an
approved
solvent and dry
thoroughly. Precautions and procedures outlined
in TM 10-1114 will be adapted to the tank.
Areas of the tank to be subjected to severe heat
must be cleaned to the bare metal; use a stiff
stainless steel wire brush or other suitable tool
for this purpose. Pay particular attention to the
seams; heat from a welding torch tends to vola-
tilize tetraethylened deposits, causing toxic
fumes. The tank exterior must be cleaned of all
dirt, sand, oil, or other foreign matter with a
solution of trisodium phosphate and water; rinse
with plain water and dry. Remove paint from any
area to be welded.
d. Welding Precautions.
(1) Completely drain all fuel from tank to
be purged; be sure the drained fuel is removed
from the area where work will be performed.
(a) Remove all fuel from floor; remove
all fuel-soaked rags and waste from area.
(b) If electrical welding is to be perform-
ed, be sure you have adequate shielding to pro-
tect other workers from injury.
(c) This process is to be undertaken by
field and depot maintenance units. Supporting
agencies will furnish additional skills and equip-
ment when required.
6-10
(2) Essentials:
(a) Efficient purging of fuel tanks, pipe
lines, pump housings, hoses, and distribution
manifolds may be accomplished by adherence to
procedures outlined herein.
(b) Materials required:
1. Adequate source of water with a
large diameter hose long enough to reach the
vehicle or fuel tank.
2. Compressed air source and air hose
of sufficient length to reach depth of fuel tank.
3. Sufficient quantity of gas tank purg-
er obtainable through local procurement. Only
known source available to date: Product-Sol, Inc.,
2010 Cole, Birmingham, Mich.
(3) Safety precaution:
Warning: Prior to and during all operations
outlined in this bulletin, coordinate with safety,
medical, and fire departments to comply with
safeguards contained herein and other applica-
ble directives.
(a) The tank being purged must have a
static ground during all operations; caution
should be taken with all tools and metal objects
around tank to insure no contact of sufficient
force is made to create a spark.
(b) Conduct a combustible vapor test read-
ing prior to purging the tank, using an accep-
table explosive meter, such as MSA explosive
meter 6665-664-4650 or Davis Vapotester 6665-
562-8103.
(c) Only competent personnel, thorough-
ly instructed in the proper handling and reading
of the vapor-indicating instruments (explosion
meter), will perform vapor tests.
(d) Conduct a combustible vapor test
reading immediately after purging. Under no cir-
cumstances will repair of fuel tank begin until
declared safe by safety personnel.
(e) Discontinue all operations if an elec-
trical storm is threatening or in progress.
(f) Eliminate all possible causes of ex-
plosion.
(g) Personnel engaged in purging opera-
tions will:
1. NOT wear wool, nylon, silk, rayon
or other similar static electricity-generating cloth-
ing.
2. Wear clean cotton clothing with no
metal buttons or
from pockets.
fittings. Remove all contents
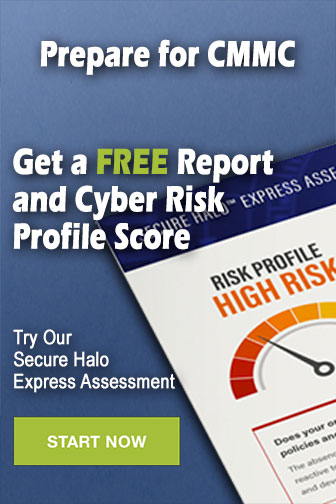